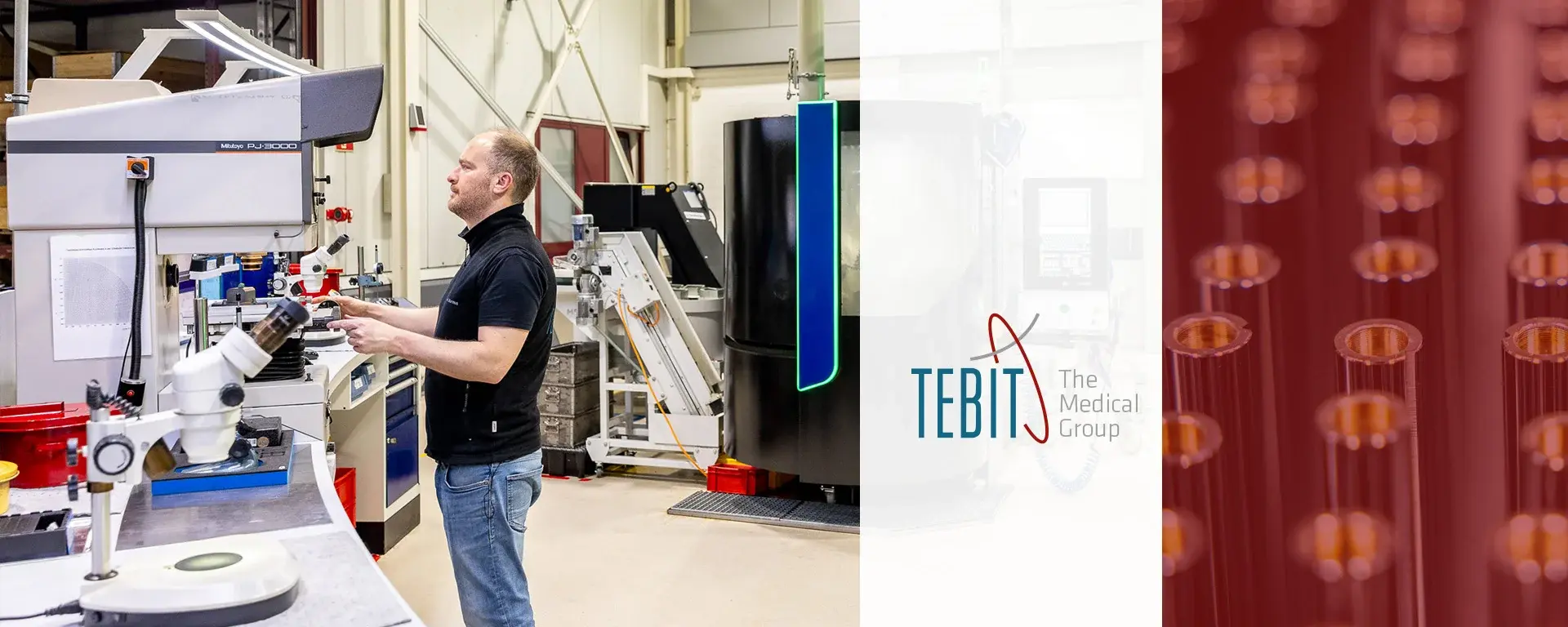
Quality that Gets Under Your Skin
Medical technology places particularly high demands on the quality of products and processes, as even the smallest errors can have serious consequences for patient safety. TEBIT – The Medical Group is a renowned manufacturer of components and assemblies for medical technology, including dental implants and bone screws. Accordingly, the company relies on the highest quality standards to ensure the safety, durability and performance of its products – and it depends on a reliable quality partner for this. In the case study, you can read how TEBIT ensures quality in all areas with Babtec software and leaves nothing to chance.
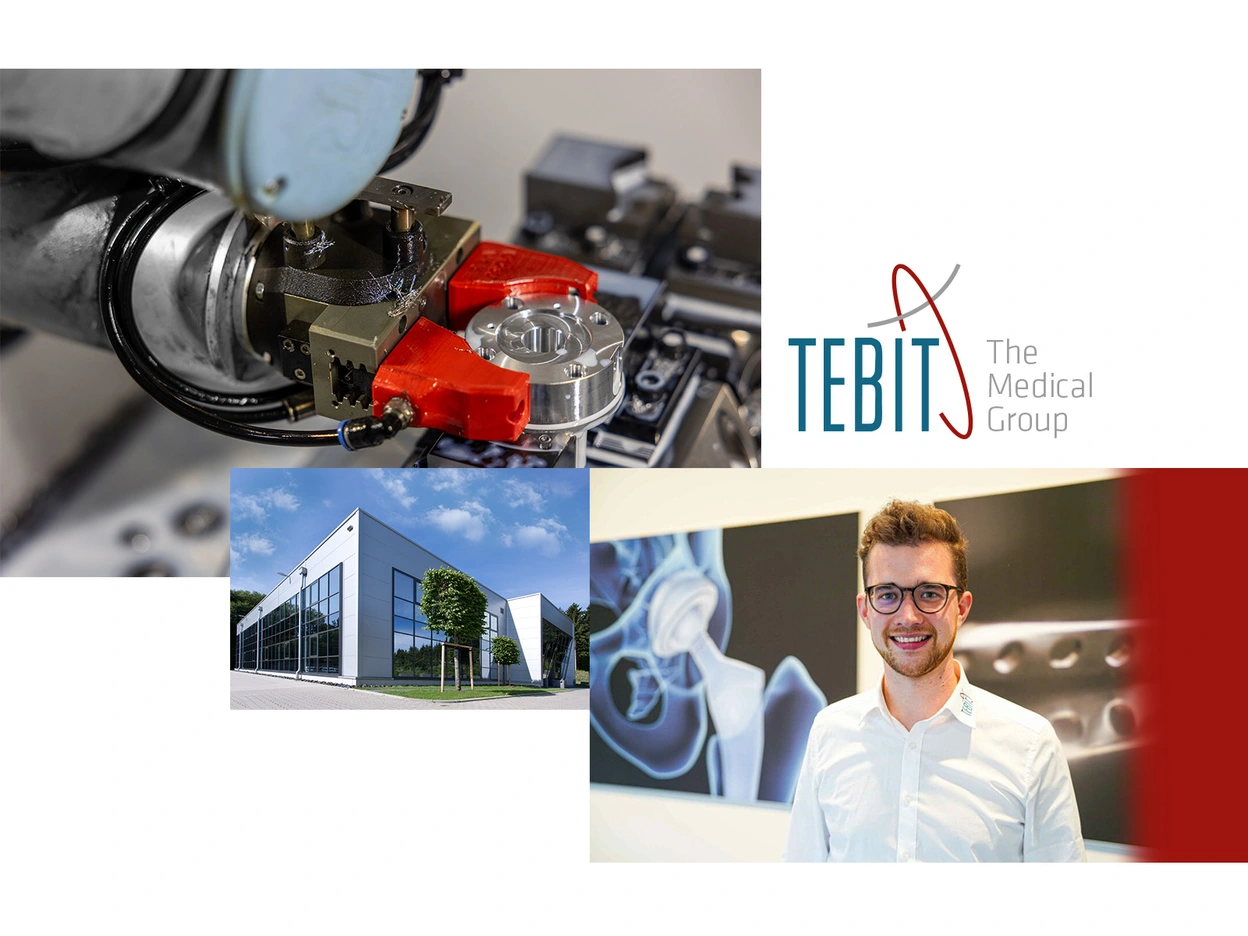
High Requirements, High Self-Demands
TEBIT – The Medical Group pursues a strict quality strategy based on internationally recognized standards. In particular, this includes certification in accordance with ISO 13485 (which is specifically tailored to quality management for medical products) – it ensures that all processes, from development and production through to final inspection, meet the highest requirements. A central component of quality assurance at TEBIT is comprehensive documentation and traceability. Every material used and every process stage is precisely logged to ensure complete traceability. For the Meinerzhagen-based company, however, this is not just a regulatory requirement, but also an essential factor for the sustainable improvement of its own products.
TEBIT relies on strict process controls because the company operates as a critical supplier in the medical technology sector and, as such, bears a special responsibility as the products are essential components of medical devices and implants. A failure or quality deviation can have a direct impact on safety and warranty in practice. For this reason, regular tests are carried out during production to ensure that each product meets the defined specifications. This continuous quality assurance ensures that faults are detected and rectified at an early stage, which increases the efficiency and reliability of production and meets the high demands of the industry. However, it was precisely these high quality requirements that meant that manual maintenance of the processes was simply no longer feasible at a certain point. The complexity and the need for complete traceability in medical technology required the use of a specialized software solution with which TEBIT was able to meet these challenges and establish efficient, digitally supported quality assurance.
Faithful Companion for Quality
TEBIT has been relying on Babtec software for over 20 years to efficiently fulfill all quality requirements. The solution enables systematic and digital quality assurance through comprehensive process monitoring, documentation and analysis of quality data. With the help of Babtec, sources of error can be identified at an early stage and continuous improvements can be implemented.
Against this background, one particular area of application for the Babtec software at TEBIT is cleanroom packaging. This is a specially regulated process in which products are packaged under controlled conditions to ensure maximum purity and sterility. This is particularly important for dental implants and bone screws that are inserted directly into the body. Babtec software supports TEBIT in this by controlling correctly set sealing machines, monitoring cleanroom cleaning and measuring airborne particles. This ensures that all cleanroom specifications are adhered to and documented.
In addition, TEBIT uses a wide range of software modules from Babtec to optimize quality assurance – including test planning, test equipment management, complaints and supplier management. In the context of supplier evaluation alone, the company was able to reduce the time required immensely: whereas before using Babtec it usually took half a day to manually maintain the supplier evaluation, this process now only takes about an hour with the software support, which corresponds to a time saving of over 75 percent. All the modules used enable systematic control and monitoring of quality along the entire value chain and ensure efficient handling of quality processes.
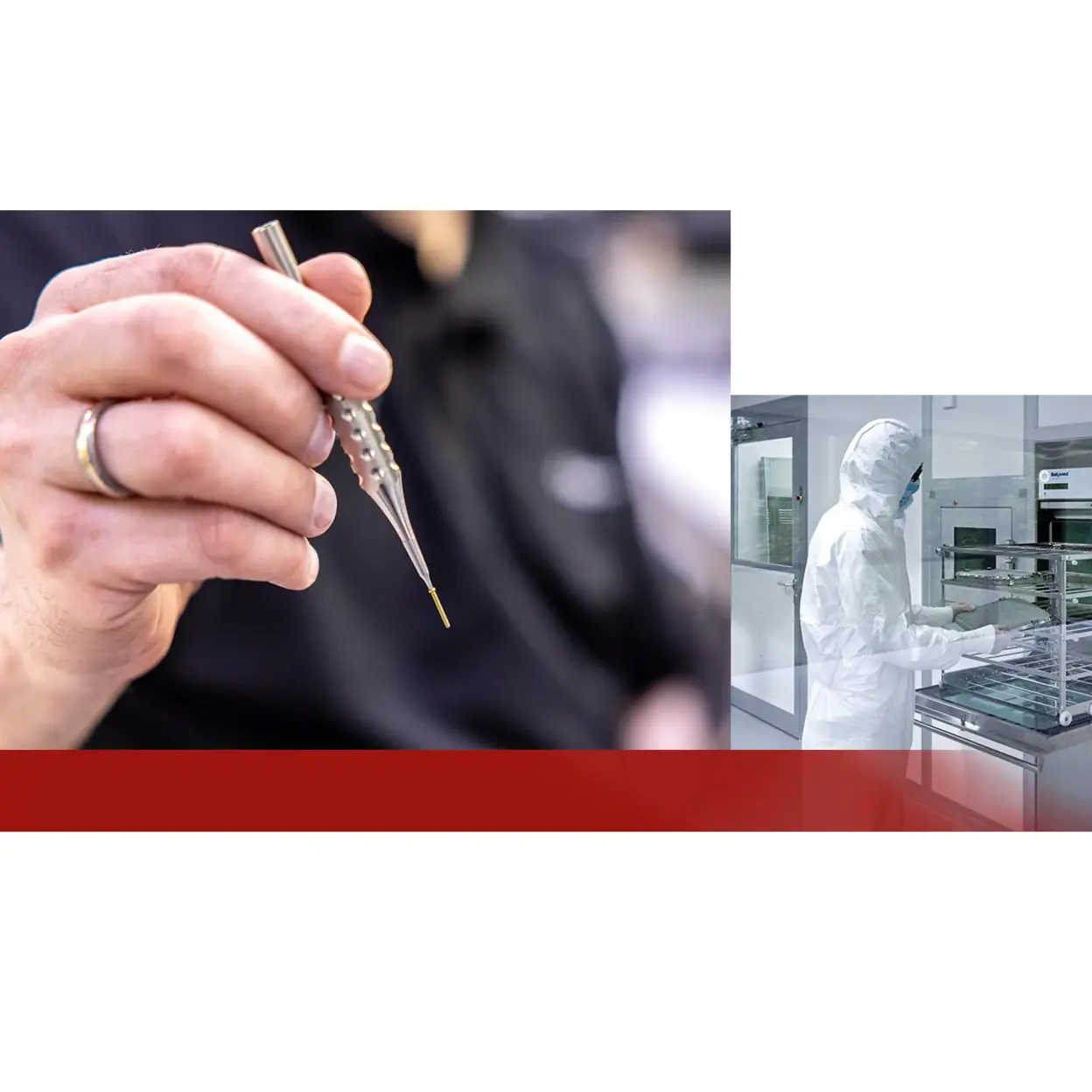
Proactive Action Is the Key
Another central module that TEBIT uses intensively is CAPA management (Corrective and Preventive Actions). This helps with the sustainable elimination of problems by systematically supporting the root cause analysis of quality deviations and initiating corrective and preventive measures. While FMEA (Failure Mode and Effects Analysis) proactively identifies and evaluates potential sources of error in advance in order to proactively minimize risks, CAPA management is used to analyse and eliminate errors that have already occurred. Especially in medical technology, where product and production errors can have serious consequences, structured CAPA management is essential. TEBIT uses Babtec software to check the effectiveness of the measures and ensures that similar errors are avoided in the future.
In practice, this looks like this: The entire CAPA process is mapped in a transparent and standardized way and in so-called SOPs (Standard Operating Procedures), the responsible employees define which rules, events or key figures should trigger a CAPA process. If there are already complaints about a product or if deviations have been identified in an audit, users take advantage of the integrated Babtec solution and refer directly to the relevant processes in the other modules within the CAPA project. This preventive error avoidance leads to a significant and, above all, sustainable improvement in process stability and quality.
Reliability Since Day One
TEBIT – The Medical Group deliberately relies on consistent quality assurance that encompasses all areas of the company. Through certifications, process controls, employee training and compliance with international standards, the company ensures that its products meet the highest quality requirements. With the help of Babtec software and the end-to-end integration of the modules, quality processes are digitally controlled, optimized and continuously improved throughout the entire product creation process. In particular, the use in the area of cleanroom packaging and the CAPA module help to ensure the highest quality standards and prevent errors – so that customers can rely on the quality delivered with a clear conscience.
This consistent approach is also reflected in the IT landscape. At the beginning of 2025, TEBIT fundamentally restructured its software landscape – with one exception: Babtec. While other systems were replaced, Babtec remained as the central solution. The reason for this lies in the user-friendliness, clear modular structure, end-to-end integration and broad usability of the software. Babtec also offers excellent documentation and interfaces to BI systems and the ERP system. In this way, TEBIT ensures that the QM processes remain seamlessly integrated into the company structure and can continue to be carried out at the highest level. In an industry where quality determines life and health, TEBIT makes no compromises and sets standards in medical technology with Babtec as a quality partner.
Comments
No comments