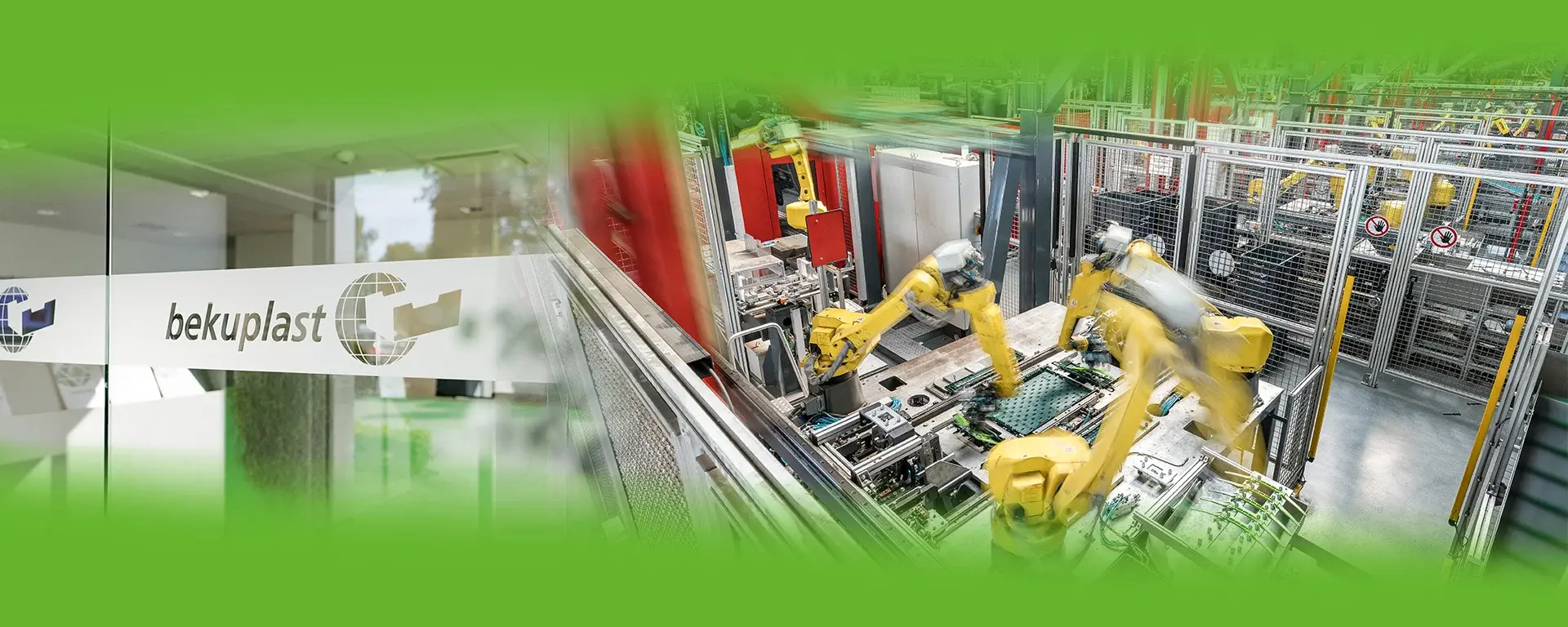
Logistics Rethought
Whether transport containers, pallets or folding boxes: bekuplast GmbH offers customized reusable transport packaging for efficient and sustainable logistics processes. Even in the daily, diverse use of the products, it becomes clear that not only a high level of quality but also innovation is important in production. In the case study, the plastics manufacturer describes how Babtec's software is helping to continue the company's success story.
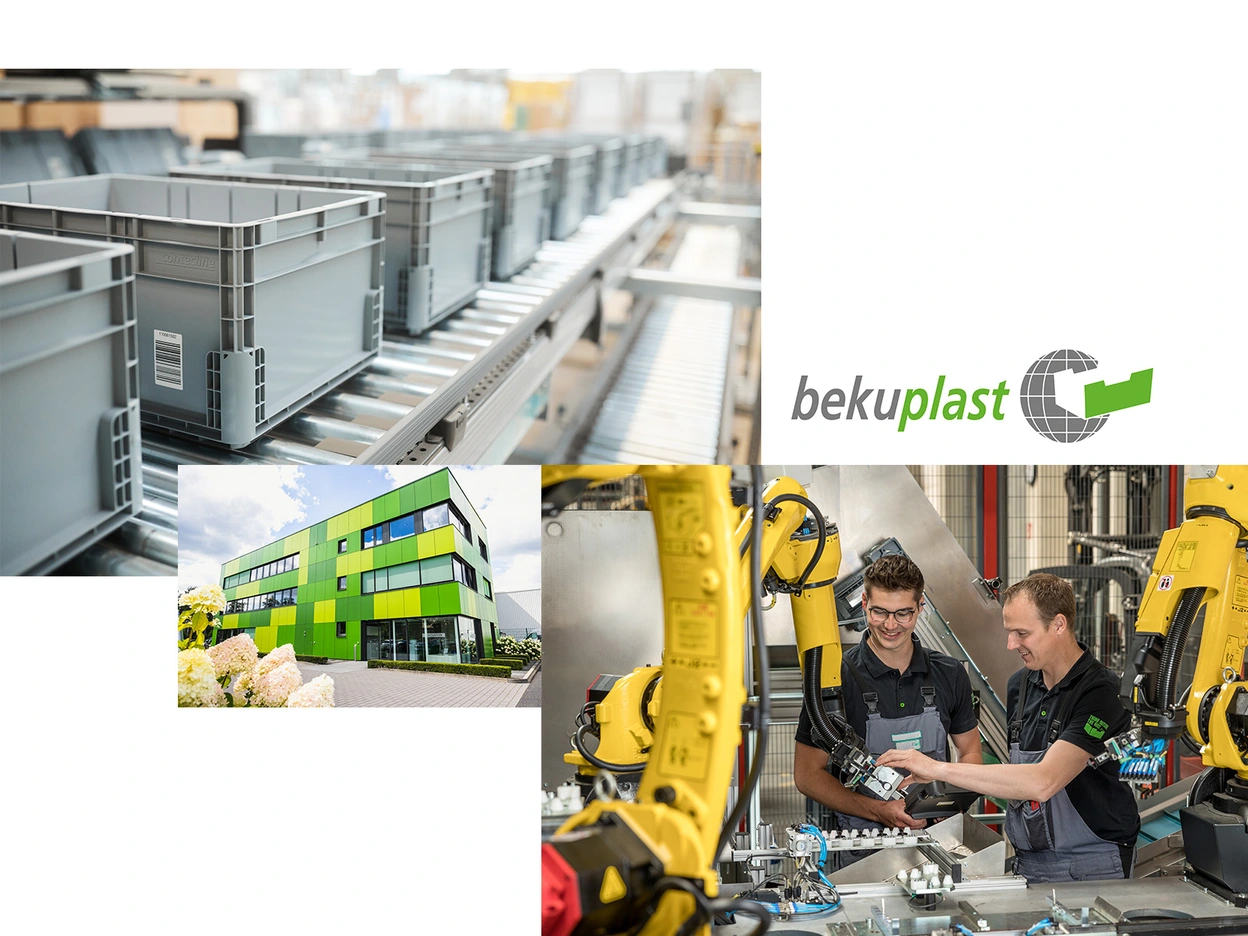
Bekuplast GmbH is one of the leading manufacturers of reusable transport packaging in Europe. Since its foundation in 1985, the company has developed from its origins in the agricultural sector into a versatile supplier – with products for retail (supermarkets and DIY stores), intralogistics (in-house logistics) and the pooling industry (joint use of resources to increase efficiency), among others. Headquartered in Germany, bekuplast develops, produces and sells plastic containers, trays and pallets that are used in a wide range of industries. And most of us have certainly already come into contact with these products in everyday life.
With a clear focus on sustainable plastic solutions, bekuplast is setting new standards. But this development is no coincidence: over the years, success has primarily been the result of close collaboration with customers. Together with bekuplast, solutions are developed for a wide variety of challenges and applications, whereby all properties are taken into account individually – from specific models to series production. Custom-made products are the company's core business, which in turn was a reason to take the next step in quality assurance and process automation.
Choosing the Right CAQ Tools
What had been looming for some time became a reality in 2014: bekuplast realized that increasing quality requirements and more effective complaints management called for new software. First and foremost, a good connection to existing measuring systems and machines was crucial so that the new solution could be integrated as seamlessly as possible into the existing process landscape.
Barely a year later, after an intensive comparison, bekuplast finally introduced Babtec's QM software in order to map inspection plans in the first phase, process measures centrally and organize complaints management efficiently. The implementation of the Babtec software went remarkably smoothly. Under the management of bekuplast's IT department and with constant support from the Babtec experts, the systems were set up quickly. Despite initial minor problems with the machines, the rollout was completed without any delays.
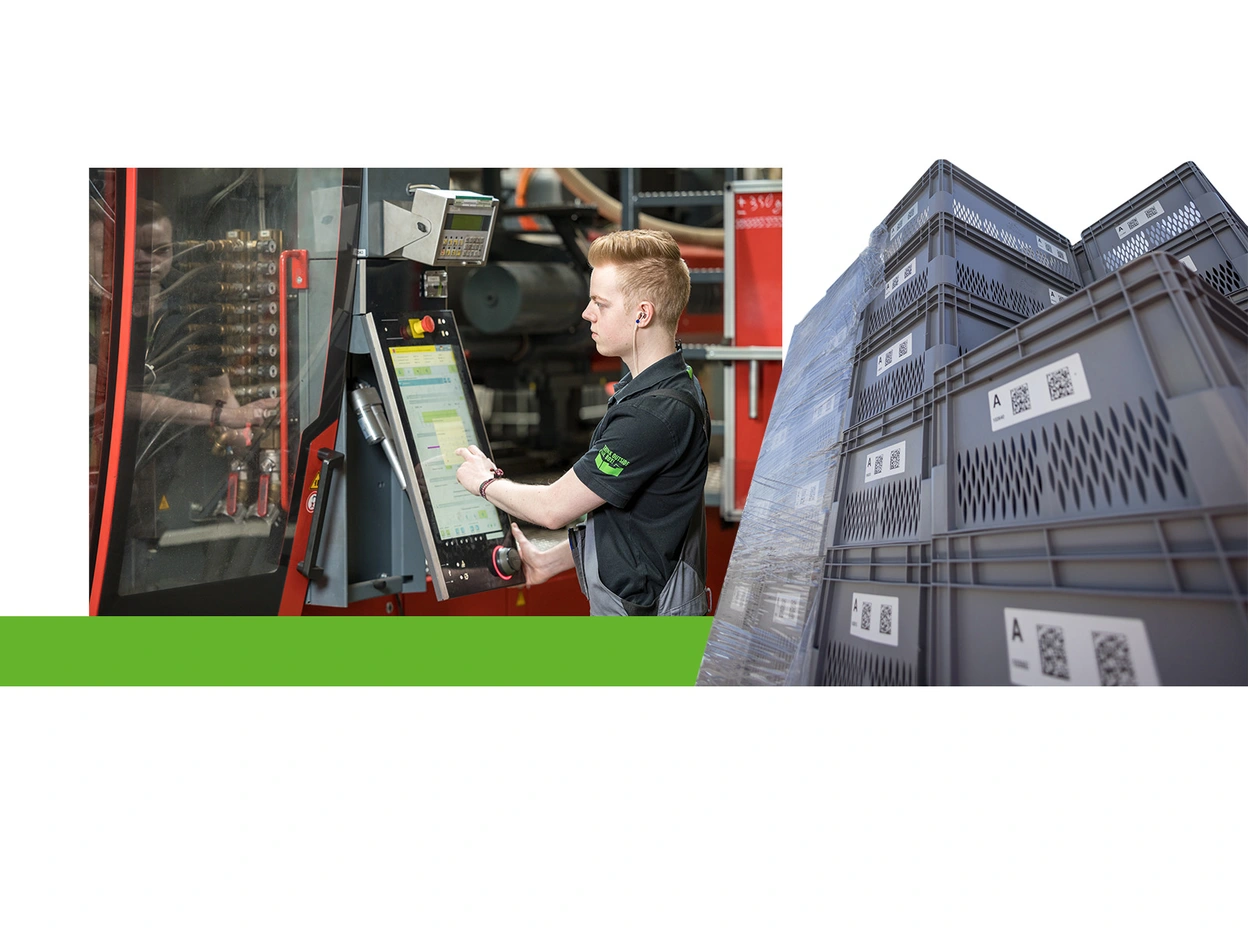
The Magic Word Is "Connectivity"
The company's quality assurance department has been working intensively with Babtec's software ever since, with the seamless integration of interfaces to measuring devices such as Faro measuring arms and now also Zeiss laser measurements playing a central role, as already mentioned. The measurement data is transferred directly to the Babtec software and analyzed there. Despite the fortunately low number of complaints, these are processed professionally both internally and externally, with BabtecQ Go – the browser-based front end – allowing non-departmental employees, e.g. from sales, to be directly involved in the process.
However, the Babtec software at bekuplast is not only connected to the measuring machines, but also to important company systems such as ERP, MES and PDA. These interfaces enable a seamless exchange of master data with the Babtec software, giving employees an insight into the current production status. Through regular updates, the software makes it easier to decide whether a new inspection is necessary, which in turn contributes to the continuous improvement of quality.
Focus on Sustainability and QM
At bekuplast, quality is not just a compulsory task, but a central corporate value that runs through the entire organization and shapes day-to-day work. Quality targets are set together with the management and continuously monitored throughout the year. Quality always takes precedence over price and is not only anchored in individual departments, but also deeply in the DNA of the company and its management.
In this context, the Babtec software has proven to be indispensable for quality assurance at bekuplast. The newly introduced complaints management system has not only shortened processing times, but has also contributed to the continuous improvement of processes. Digital traceability means that no action is lost or remains unprocessed. And it supports the sustainable elimination of errors, so that the few complaints are reduced even further over time.
But the Babtec software also supports bekuplast in efficient quality management beyond complaints. In addition to successful internal auditing and certification, the company also prioritizes continuous improvement management (CIP). Site inspections and the associated use of checklists lead directly to measures and tasks that are digitally recorded and tracked centrally. Employees at the plant are given specific inspection tasks, such as checking the container weight, which reduces the reject rate. Thanks to the clear assignment of measures and the sustainable elimination of causes, no steps go unnoticed, which favors the continuous improvement of processes.
A Future Characterized by Quality
It is pleasing to note that the standard version of the software is used for the most part. Only in very rare cases did bekuplast have to rely on customizations, which were then implemented quickly and efficiently by the Babtec team. This was in line with the company's aim of viewing the software as the center of its quality work from the outset and aligning its processes with it.
The integration of the Babtec software into bekuplast's processes was a strategic milestone: with improved quality assurance and effective complaints management, bekuplast has strengthened its competitiveness and consolidated its customer relationships in the long term. The upcoming expansions promise to continue this success story and continue to position bekuplast as a pioneer in the industry.
Looking to the future, bekuplast is planning, for example, to optimize supplier monitoring with the Babtec software supplier cockpit. Occupational safety is also to be further structured through HSE (Health, Safety, Environment) measures via Babtec – the first HSE measures are already being mapped via Babtec today. Checklists and inspections will also help to identify and eliminate hazards more efficiently in the future so that the entire company is optimally equipped to meet the individual requirements of customers and standards. In addition, preventive maintenance for monitoring machine performance and avoiding faults could also become interesting in the near future. One thing is certain: the successful co-operation between bekuplast and Babtec and the effective expansion of a comprehensive quality management system have only just begun.
Comments
No comments